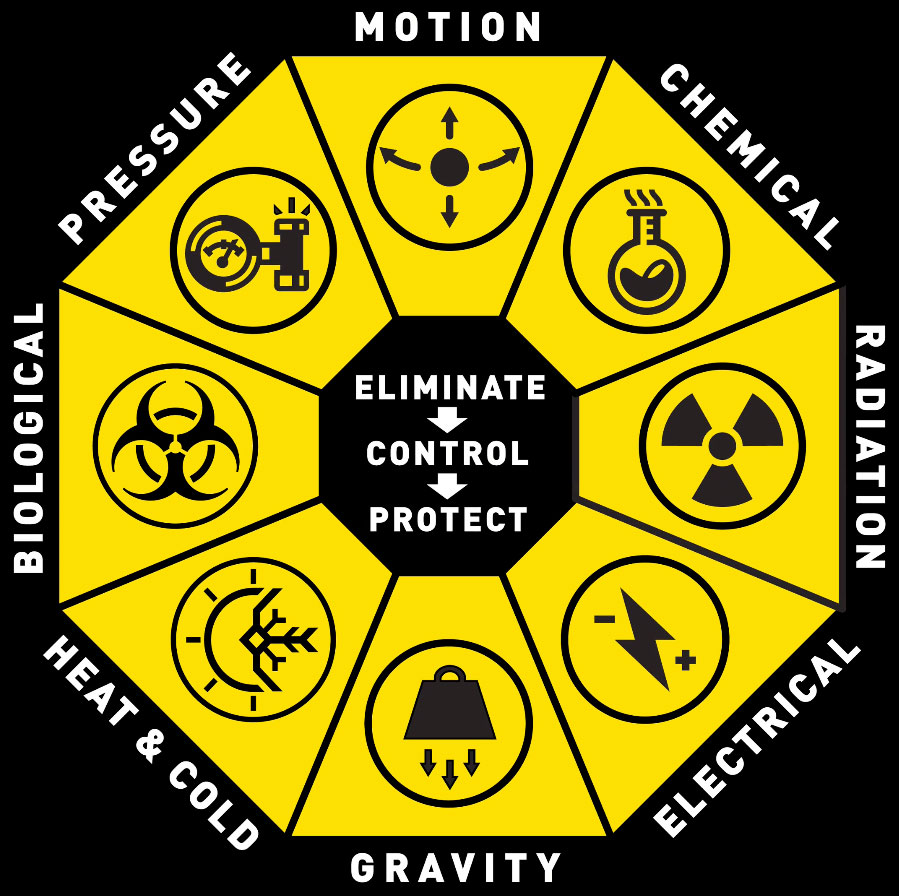
Transform your safety approach with Hazard Recognition Plus (HRP), an innovative, human-based process that focuses on energy sources as the foundation of work. Unlike traditional risk assessments that only look at hazards, HRP identifies the energy sources that create these hazards, allowing us to manage and prevent them from entering the workplace.
Hazard Recognition Plus TM at DuPont
Why is recognising hazards important?
Identifying hazards is the fundamental component needed to protect our workers. It goes beyond safety to encapsulate every aspect of the work a business performs.
Workers cannot manage what they do not recognize. Workers do not perform tasks expecting to get hurt, if they see the hazard they will manage it.
How can businesses improve?
A multitude of programs and processes are developed in an effort to manage risk. Yet incidents continue to happen, because all of these rely on managing ‘anything or something with the potential to cause harm’, which is how industry around the world defines a hazard.
By looking beyond the traditional view of hazards towards a more progressive understanding of how hazards are formed, energy.
HRP helps businesses establish a common language which ensures levels of planning reflect accurately the risk of the job. Using a common language to perform ‘energy based’ observations ensures quality interactions take place, and ultimately a safer, more efficient and productive operation
The difference.
-
- Employees grow in competence in identifying hazards and therefore increasing their ability to control them
- Leadership actively engages in meaningful interactions with the workforce
- Job planning and work discussions grow in quality
-
- Increased reliability
- Reduction of waste
- Increased production
Results
Our Approach
Phase 1 – Define
Phase 2 – Engage
Phase 3 – Sustain
Contact Us
Take the first step in transforming your business safety culture and speak with one of our solutions exports today.